LIFE VIABLE Project
Valorization of lignin bIomass into competitive components grAdually replacing BPA in the formuLation of Epoxy resins
Objectives
The overall objective of the LIFE VIABLE project is to reduce the environmental and health impacts of BPA by lowering its content in the formulation of epoxy resins by 20 to 50%.
To do so, project beneficiaries will pursue the following Specific Objectives (SO)
SO1: Demonstrate the technical, environmental, and socio-economic performances of a future viable alternative to BPA in epoxy resins for high performance applications
LIFE VIABLE will demonstrate the feasibility of integrating Glycidylated Lignin Oil (GLO) in epoxy based composite materials to manufacture 2 car components (one structural, one aesthetical). The final products will have technical characteristics similar to commercial materials (e.g. Tg≥100°C) and improved environmental and socio-economic impacts.
SO2: Reduce the residual emissions of BPA and workers exposure related to epoxy resins production by 20 to 50%
As a result of SO1, the residual emissions of BPA in industrial surroundings, i.e. surface water, soil and air, as well as workers exposure linked to the production of epoxy resins will be decreased by up to 50% in production facilities.
SO3: Adapt industrial processes of the whole value chain for the large-scale production of LIFE VIABLE composite material
As the environmental issue is tackled from the source (i.e. raw material), all steps of the value chain will be impacted. LIFE VIABLE will demonstrate adaptations of the current industrial processes so that results can be integrated into existing production chains. End-of-life will also be carefully studied.
SO4: Widely disseminate the project results towards end-users, policymakers, chemical and biomass industries
At least 4 sectors and some representatives of industries using epoxy resins will be reached, as well as policymakers, providing them with an example of future substitution to be fostered.
SO5: Prepare the market penetration and exploitation of the solution
LIFE VIABLE intends a quick commercialisation of its solution, supported by the participation of international companies such as SYENSQO and CRF. Market entry activities will be run during the project, as well as the anticipation of improvements to go further in the substitution of BPA by GLO. Replication to at least 2 other automotive components and transfer to 4 sectors will be studied.
Main results
To answer all these objectives, you can see below all the actions that will be implemented in the LIFE VIABLE project.
[Done] [in progress] and [not started] will be used to track the progress of each action.
Preparatory actions
Techno-economic specifications
In the LIFE VIABLE project, two use cases have been selected from a list of potential epoxy-based car applications to be fully developed with our lignin-epoxy resin system: one structural and one aesthetic part.
It goes without saying, but when a product is being developed based on a new resin system, it is important to respect a certain number of specifications. This is particularly the case with biobased resins.
For the targeted products, the main requirements are mechanical resistance, thermal resistance, chemical resistance, long term properties, the end-of-life scenario, the toxicity and last but not least, a range of acceptable cost targets considering the whole value chain.
Another crucial aspect to be considered in elaborating the design specifications for the resin systems is the manufacturing process. Indeed, it is broadly recognized that design, material selection and manufacturing are closely related activities that cannot be performed in isolation of one other.
In particular, the material design must consider the manufacturing process to be used. Therefore, it is crucial to perform a straightforward description of the specifications for the manufacturing process/es.
In this task, HPC, as the composite manufacturer, defines which manufacturing process/es should be used to produce the two car components and provides all the needed information to guide the new materials development activities.
Raw materials
One of the essential first steps in this project is to precisely define the specifications of the raw material, in this case lignocellulosic biomass. Criteria such as availability, composition, in particular the lignin yield, and the process of lignin extraction are foreseen.
In addition, the selection of the feedstock will also be oriented by the intrinsic lignin characteristics, such as its functionality (hydroxyl content, aliphatic ether content, etc.) which strongly depends on the lignin source and can affect the lignin processing (extraction/depolymerization/derivatization).
Based on requirements from VITO for the depolymerization and the criteria required to apply the extraction process, CIMV defines the raw material specifications to comply with those requirements.
Then, CIMV selects the most relevant feedstock source(s) fitting these requirements: the main targeted raw materials can, for example, be agricultural residues, such as straws for their availability and their processability but also woods for their lignin chemical structure. Depending on the interest, other specific lignocellulosic material can be considered.
Specifications of the monitoring and impact calculation methodologies
When trying to find a solution to replace fossil-fuel based materials such as BPA, it is important to investigate if the solution does not bring other issues. In this case, APESA will carry out a study on the environmental impact of lignin production and its processing for use as a component of epoxy resins.
The LIFE VIABLE value chain includes within the consortium a bio refiner, a specialty chemical manufacturer , a composite manufacturer and a car manufacturer. All of them are connected to bring to market products derived from bio-based resources.
However, other stakeholders can join the LIFE VIABLE value chain in order to evaluate replicability and transferability of the technologies. For instance, it could be relevant to investigate the transfer of LIFE VIABLE lignin-based intermediates to the construction, marine and aerospace sectors.
(In case you would be interested in joining and willing to exchange information about requirements for products from these sectors, please don’t hesitate to contact us.)
A search for scientific publications on Life Cycle Cost of epoxy resins (including bio-based alternatives) will be carried out in order to collect elements of reference and comparison to what will be achieved in the LIFE VIABLE project.
Implementation actions
Production of organosolv and depolymerized lignin
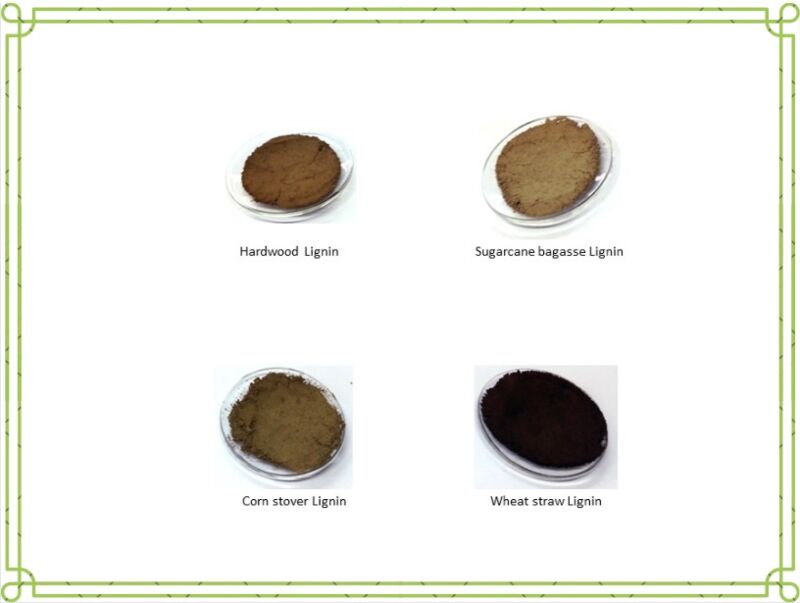
The production of organosolv lignin is dealt with by CIMV. First, lignin from promising feedstocks will be tested on small scale. Then, the best lignin candidate will be produced at large scale, in order to deliver enough material to VITO for the next steps. This will be achieved thanks to the CIMV pilot plant.
The first lignin samples delivered by CIMV will help optimize the depolymerization conditions (depolymerization time, amount of catalyst, solvent used, etc.).
Then, the most industrially relevant conditions will be applied to the selected lignin candidate and further optimized, regarding the properties of the targeted epoxy resins. If the properties and processability (i.e. solubility) of epoxy resins is not good enough, the depolymerized lignin characteristics will be tuned to further deliver on the resin performance and ease the prepreg manufacturing.
Characterization of biomass is often a big challenge, due to the high complexity of the natural product. However, it is crucial for further production of lignin-based intermediates.
VITO will therefore work on the advanced lignin characterization, focusing mainly on the measurement of dispersity using gel permeation chromatography and hydroxyl content using 31P NMR. In addition, solubility analyses of the optimized depolymerized lignin fractions will be done to ensure further processing at larger volumes is possible.
Finally, VITO will perform toxicity and ecotoxicity tests of the produced lignin. Methods in line with REACH registration requirements will be applied.
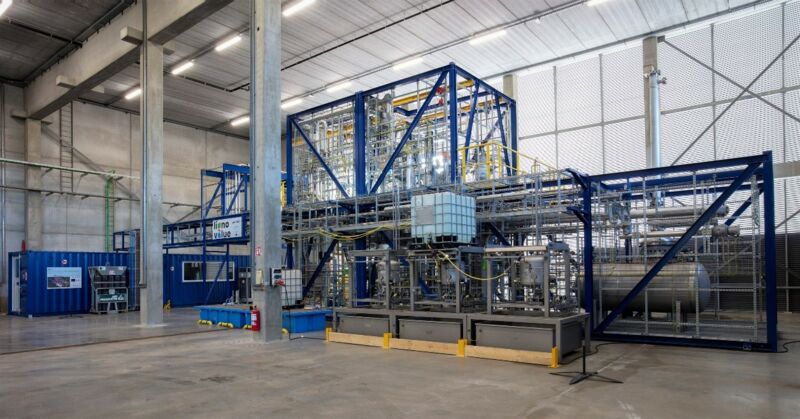
VITO will produce depolymerized lignin according to parameters defined previously, from lignin feedstock provided by CIMV.
The production capacities will be increased all along the project, from lab scale (few grams) to production (hundreds of kilograms) using the LignoValue demo facility.
Demonstration of the production of lignin-based intermediates
To obtain lignin epoxy resins, epoxy functionalization (glycidation) of depolymerized lignin is required. In this regard, VITO will work on reaction conditions investigating the effects of reaction temperature, ratio of reagents and reaction time to optimize and obtain the most efficient and economical route possible,
Once the glycidation reaction conditions defined, the first samples of glycidated lignin will be produced by VITO and evaluated by SYENSQO in a resin formulation. Back and forth validation by VITO and SYENSQO is necessary to select the best GLs.
Based on the previous results, WESTLAKE will further develop the glycidation process so that large scale production is feasible from a techno-economic point of view. WESTLAKE will investigate the reaction and work-up (post reaction) phases to streamline the manufacturing process. WESTLAKE intends to demonstrate the large-scale production of the Glycidated Lignin, starting from a few kilograms up to several hundred of kilograms.
Similar to the depolymerization process, the glycidated lignins will be characterized by WESTLAKE in order to evaluate the success of the glycidation reaction on the lignin feedstock.
Characterization of the samples will be based on GPC, FTIR, 31P NMR, epoxide and chlorine content titrations.
In addition, VITO will carry out acute and chronic toxicity and ecotoxicity tests on samples of GL to prove its safety and will determine its physico-chemical properties to assess its environmental fate and end-of-life behavior.
Formulation of epoxy resin and demonstration of its integration in manufacturing process
When introducing a new compound into a formulation, compatibility can be an issue. Thus, the BPA epoxy monomer that constitutes the resin of reference will be replaced partially, by the glycidated lignin. In the LIFE VIABLE project, the objective is to start from 20 weight % of the overall resin and increase further if possible.
At the beginning, the formulation (BPA + GL) will be prepared at lab scale (i.e. 20g scale). Reactivity will be studied and property measurements will be achieved through DSC, DMA, TGA and rheology experiments. These characterizations will allow feedback to VITO and to WESTLAKE in order to recommend the best GL candidate for the scale up.
From the GL candidate selected by VITO, WESTLAKE and SYENSQO, epoxy resins will be formulated in a reactor. Thus, SYENSQO will be able to study the neat resin properties and processability as a function of GL content.
Several compositions will be prepared. SYENSQO will select other resin components to optimize resin reactivity, process and properties to match the characteristics of the epoxy resin of reference and allow for industrial scale up. Upon investigation SYENSQO will exchange feedbacks with VITO and Westlake, to prepare on the manufacturing of GL.
Pilot trials will be performed and the prepreg manufacturing conditions will be established around resin filming and impregnation of carbon fiber fabrics. The film will be prepared from the selected epoxide resin formulation in step 3.2. to a control areal weight. In a second step, this film will then be combined with a carbon fiber fabric to produce a prepreg, with controlled resin content.
A 6-month period is required to assess the exotherm hazard on the resin, optimize the manufacturing conditions and evaluate the properties of cured laminates.
This is the last step for the industrial production of prepregs, starting with the manufacturing of several hundred of kilograms of resin, follow by the production of two films and therefore two different real weight prepregs which will allow the manufacturing of the two car prototypes by HPC and CRF.
Two films and two prepreg types (200 sqm in total) will be produced following the production conditions optimized in the previous section within 2 to 3 months.
Design, realization and optimization of the composite materials
In addition to the development of new materials, LIFE VIABLE aims to create new product concepts. For this reason, starting from the results of the previous tasks and in close collaboration with the next steps, HPC will start designing material stratifications for the two use cases defined previously. These stratifications will be developed both from a structural and aesthetical point of view and with regards to the process parameters.
In particular, the geometries, and mechanical and technological characteristics required of car components for the validation of the new materials will be analyzed by HPC and CRF.
During this step, the main objectives are:
- to develop a reliable production process that minimizes cycle times, costs and defects of products made with the new materials
- to produce samples to be tested.
The production process, in addition to having a direct influence on the design of the component, is closely linked to the material from which the component will be made. In particular, the behavior of a material is not only a function of its properties but is also strongly influenced by the manufacturing process. This intimate relationship between process, product and materials makes it necessary to take into consideration all these aspects.
HPC will then determine the parameters that optimize production processes, save costs and development time. In particular, the optimization of process parameters such as pressure, temperature and time will be considered and measured to define the optimized configuration that will enable the process to meet the requirements defined previously.
Other objectives such as flexibility, productivity, automation, safety, environmental impact, quality, maintenance, process control, etc. will be considered in the perspective of industrial production.
Once optimized parameters have been defined, technological tests will be carried out by HPC with the aim of verifying the optimized process parameters.
These processes will be used in the next steps, ensuring the production of parts with low levels of defects and performance as defined at the beginning.
At least 10 different stratifications, made from the previously developed resins, will be investigated, and tested by CRF and HPC to find the most outstanding solutions in producing bio-composites for automotive applications.
Several key aspects of the different combinations will be analyzed by CRF and HPC, through physical experimentation, including mechanical properties, physical-chemical properties, long-term performance, moisture absorption, fire resistance, durability, property variations, sensitivity to temperature and UV radiation, processing temperatures, compatibility with the most used fabrication processes, etc.
Another crucial activity will be the study of the stability of the component over time. At first, it will be important to define the aging conditions to which the component will be subjected. Then, based on the requirements defined previously, CRF will carry out experimental tests to investigate how the materials developed behave in response to UV rays, thermal cycles, humidity cycles at different concentrations.
The main material-related critical aspects will be improved by means of different methods and tools including, but not limited to, application of coatings, fiber surface treatment technology, incorporation of additives, design solutions, hybrid solutions, multi-material solutions, etc.
Based on the previous results, HPC will revise and optimize the material stratification designs for the two use cases to provide final formulations and process parameters to be used for prototypes.
Virtual optimization tools will be exploited targeting performance and lightweight in combination with cost models to allow both eco-sustainability and economic viability of the final solution.
Integration of the demonstrated prototypes in car manufacturing process
This step will aim at demonstrating the validity of LIFE VIABLE lignin-based materials in final products. For this reason, starting from the results of the previous tasks, two prototypes will be designed and produced (aesthetic and structural).
Two car parts will be designed and produced by HPC and CRF, together with the equipment necessary for their manufacturing, taking into consideration all the requirements previously defined. The complete geometries of the components will be defined in a detailed design.
Design activities will leverage IT enabling technologies for product design. Virtual prototyping (VP)
approaches will support interdisciplinary teams in analyzing product performance, reliability, and production costs and in the decision-making process.
This approach will make it possible to shorten the entire development cycle, improving quality and reducing costs.
The virtual models will be useful for optimizing component performance avoiding physical tests.
Therefore, after an experimental validation, simulations will be performed by HPC to reach the optimal design that guarantees compliance with end-user requirements. This analysis will lead to the definition of the final geometries of the two car components.
Homologation tests will also be performed on a numerical level by CRF to evaluate, in advance, the fulfillment of the constraints prescribed by legislation, saving costs and time for final certifications.
The mold to produce the prototypes will be designed and manufactured by HPC based on the
developed and optimized geometry of the components and on the manufacturing process specification described previously.
Each component will be produced by HPC with both the new resin systems and traditional materials for comparison.
At least 5 prototypes of each component will be realized to evaluate the repeatability of the processing and material characteristics.
The performance of the two prototypes will be analyzed by CRF through accurate pilot tests in accordance with the most appropriate standards.
The tests will focus on understanding the product characteristics to study the combination of raw materials/process in the defined applications. The analyzes that will be performed will be:
- Analysis of the mechanical characteristics: Mechanical tests will cover both those based on standards (e.g. tensile test) and others developed based on product requirements (e.g. impact test).
- Analysis of components by chemical-physical tests: The activity is aimed at understanding how the manufacturing process influences the quality of the component in terms of various macro and microscopic aspects such as the compaction of the material, the presence of voids, the fiber-matrix interface, etc.
- These parameters significantly influence the mechanical characteristics of the component and provide important information about the product. Tests such as the determination of the glass transition temperature, the void content, the density will be carried out by CRF and HPC on samples from the produced prototypes to evaluate the correlation with the process parameters. Performance of the final composites will be validated in operational environment.
The aim of the task is to verify the application of dismantling and recycling methods to the demonstrators based on the new bio-based composite in order to succeed in the re-use of basic components for other application, thus enabling a circular economy approach.
Recently, industrial technological recycling methods based on thermo-chemical processes have been developed and are able to recover the polymer matrix and the reinforcement resin and fibers from composites parts.
Through this step, LIFE VIABLE will address the dismantling procedure of the composite part to be able to easily include it in recycling process; and will verify if the two components, resin and fibers, of the developed new material can be treated as a standard material and recovered in the same mainstream.